Pneumatic and Electro-Pneumatic Application (AE-NS)
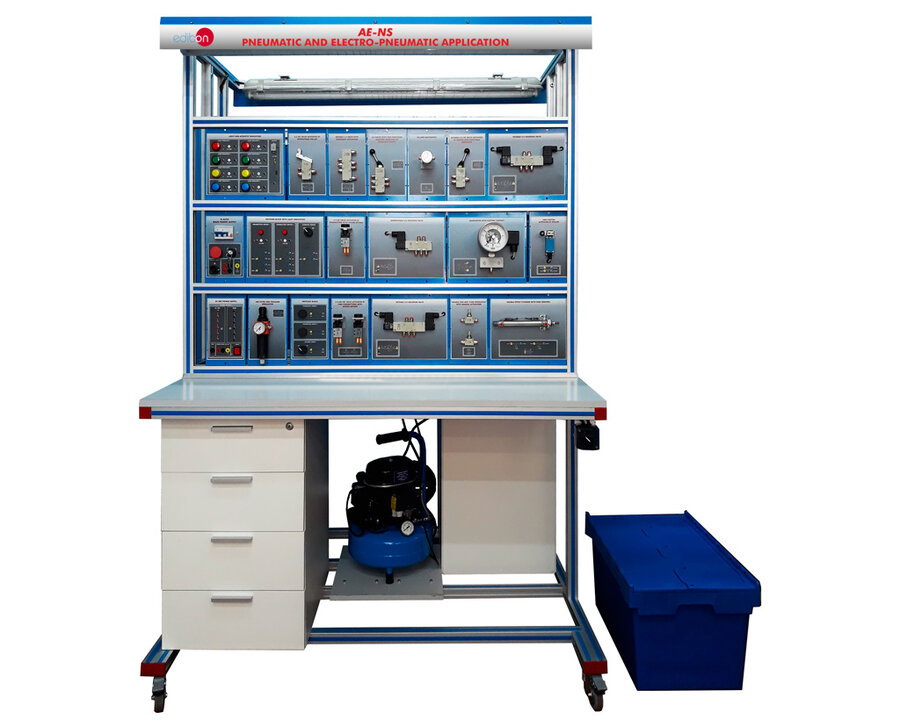

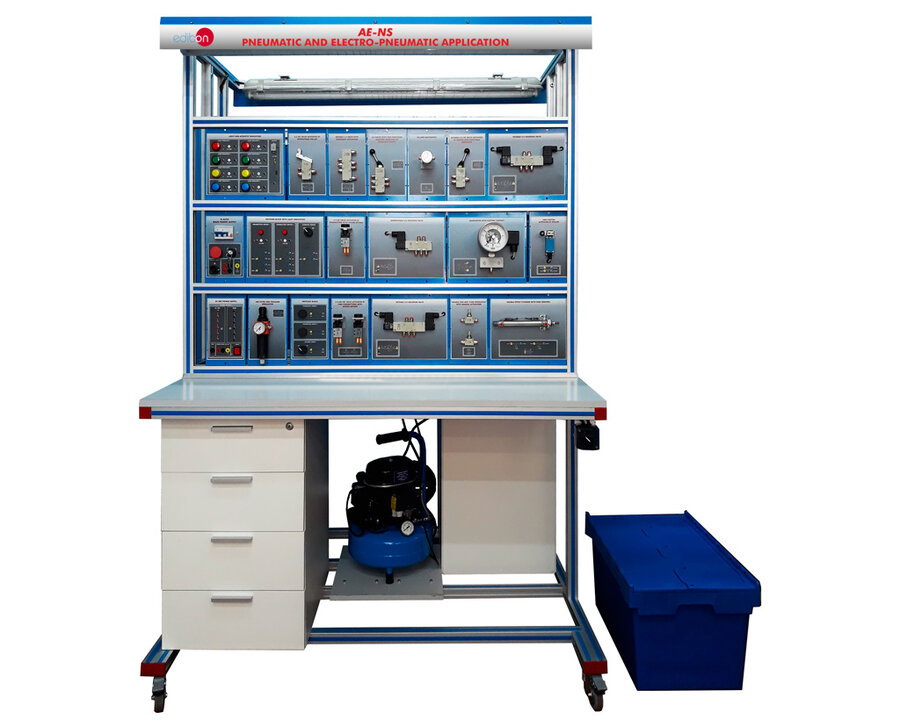
PL-403410
The Pneumatic and Electro-Pneumatic Application, "AE-NS", by EDIBON is a modular system equipped with a variety of optional kits and components, allowing users to configure pneumatic and electro-pneumatic circuits based on their specific learning or training needs.
The application offers several optional pneumatic kits designed for comprehensive studies on industrial pneumatic circuit management and operation. These kits include:
- PK-K0 – Fundamentals Kit: Contains components for basic pneumatic circuit concepts.
- PK-K1 – Advanced Pneumatics Kit: Covers both fundamental and advanced pneumatic concepts.
- PK-K1UP – Electro-Pneumatics Upgrade Kit: Adds modules to the PK-K1, enabling users to study fundamental electro-pneumatic circuit concepts.
- PK-K2 – Electro-Pneumatics Kit: Provides components for both basic and advanced electro-pneumatic concepts.
- PK-K3 – Pneumatic Actuators Kit: Focuses on common pneumatic actuators, including rotary motors.
- PK-K4 – Measurement and Proportional Control Kit: A computer-controlled kit that enables proportional control and analog signal use with pneumatic actuators, facilitating PID control via computer.
- PK-K5 – Vacuum Technology Kit: Introduces the essential components of vacuum circuits and includes various cup types for comparative study.
- PK-K6 – Troubleshooting Kit: Contains defective components to teach students to identify and troubleshoot common pneumatic issues.
For added functionality, the EDIBON PLC unit is compatible with the PK-K2 kits, enabling PLC control of pneumatic and electro-pneumatic components for advanced, hands-on experience.
Additional units are available for airflow and pressure supply, as well as customizable workbenches that accommodate one or two work areas.
- AE-NS APPLICATION:
- Work with a working air pressure of 4 bar.
- The components include Quick-Fitting connectors with Built-in Stop Mechanism for 6 mm tubing.
- Are attached to a screen printed metallic plate with the name and the standard symbol of the component.
- These metallic plates are designed to be placed on the EDIBON workbenches
Optional kits of Pneumatic components:
- PK-K0. Kit to study the pneumatics fundamentals.
- PK-K1. Pneumatics kit.
- PK-K1UP. Upgrade Kit for the PK-K1 to undestand the principles of Electro-Pneumatic.
- PK-K2. Electro-Pneumatics kit.
- PK-K3. Pneumatics Actuators Kit.
- PK-K4. Measurement and Proportional Control in Pneumatics Kit.
- PK-K5. Vaccum Technology Kit.
- PK-K6. Pneumatics and Electro-Pneumatic Troubleshooting kit.
- Cables and Accessories, for normal operation.
- Manuals: This unit is supplied with 8 manuals. Required services, Assembly and Installation, Interface and Control software, Starting-up, Safety, Maintenance, Calibration and Practices manuals.
EXERCISES AND PRACTICAL POSSIBILITIES TO BE DONE WITH THE MAIN ITEMS
PK-K0. Kit to study the pneumatics fundamentals.
- Identification of elements.
- Air compression and treatment.
- Operation of valves with manual activation.
- Activation of a simple effect cylinder.
- Activation of a simple effect cylinder from several points ("OR" valve).
- Simultaneous activation of a simple effect cylinder ("AND" valve).
- Indirect activation of a simple effect cylinder.
PK-K1. Pneumatics kit.
- Identification of elements.
- Air compression and treatment.
- Operation of valves with manual activation.
- Activation of a simple effect cylinder.
- Activation of a simple effect cylinder from several points ("OR" valve).
- Simultaneous activation of a simple effect cylinder ("AND" valve).
- Ejector function and study of the venture principle.
- Using the ejector and suction cup to grip workpieces.
- Indirect activation of a simple effect cylinder.
- Activation of a double effect cylinder.
- Indirect activation of a double effect cylinder.
- Semi-automatic activation of a double effect cylinder.
- Speed adjustment of a double effect cylinder.
- Automatic activation of a double effect cylinder.
- Timer controlled activation of a double effect cylinder.
- Accelerated return of a double effect cylinder.
- Pneumatic system with emergency pushbutton.
- Activation of a simple effect cylinder by three pneumatic signals.
- Configuration of an adjustable sequence valve.
PK-K1UP. Upgrade Kit for the PK-K1 to undestand the principles of Electro-Pneumatic:
- Identification of elements.
- Air compression and treatment.
- Activation of a simple effect cylinder.
- Activation of a double effect cylinder.
- Speed adjustment of a double effect cylinder.
- Electro-pneumatic control by a monostable 3/2 NC solenoid valve.
- Electro-pneumatic control by monostable 3/2 solenoid valve.
- Electro-pneumatic control by a bistable 5/2 solenoid valve.
- Control of a double effect cylinder using Reed sensors.
- Automatic activation of cylinders (sequence A+B+A-B-).
- Operation of a pressure switch and a manometer with electric contact.
PK-K2. Electro-Pneumatics kit.
- Identification of elements.
- Air compression and treatment.
- Activation of a simple effect cylinder.
- Activation of a double effect cylinder.
- Speed adjustment of a double effect cylinder.
- Electro-pneumatic control by a monostable 3/2 NC solenoid valve.
- Electro-pneumatic control by monostable 3/2 and 5/2 solenoid valves.
- Electro-pneumatic control by a bistable 5/2 solenoid valve.
- Control of a double effect cylinder using Reed sensors.
- Automatic activation of cylinders (sequence A+B+A-B-).
- Operation of a pressure switch and a manometer with electric contact.
PK-K3. Pneumatics Actuators kit.
- Identification of elements.
- Activation of a pneumatic linear actuator.
- Activation of a pneumatic rotary actuator.
- Activation of a pneumatic artificial muscle.
- Use the function generator to set the speed of the linear actuator.
- Use the function generator to set the speed of the rotary actuator.
- Use the function generator to set the speed of the pneumatic artificial muscle.
- Uses of different loads with a linear actuator and observe the response.
- Uses of different loads with a rotary actuator and observe the response.
- Uses of different loads with a pneumatic artificial muscle and observe the response.
- Comparison between the different actuators.
PK-K4. Measurement and Proportional Control in Pneumatics kit.
- Familiarization with data acquisition and processing of system signals from PC.
- Operation of the Background suppression photoelectric sensor from PC.
- Operation of the Polarized retroreflective photoelectric sensor from PC.
- Operation of the Diffuse-reflective photoelectric sensor from PC.
- Operation of the Fiber optic photoelectric sensor from PC.
- Proportional manual control of a proportional valve from PC.
- Analog measurement of pressure level from PC.
- Analog measurement of flow level from PC.
- PID control loop of the flow level from PC.
- Analog position sensor of the pneumatic linear actuator from PC.
- PID control loop of the position of a pneumatic linear actuator from PC.
PK-K5. Vaccum Technology kit.
- Familiarization with the vacuum components.
- Ejector function and study of the venture principle.
- Using the ejector and suction cup to grip workpieces.
- Measure of the negative pressure level.
- Regulation of the negative pressure of the vacuum circuit.
- Differences between the suction cups of the unit, and comparison of its performance.
PK-K6. Pneumatics and Electro-Pneumatic Troubleshooting kit.
- Familiarization with most common failures of the pneumatic components.
- Study a faulty air filter and pressure regulator with manometer.
- Study a faulty manometer.
- Study a faulty air pressure tank.
- Study a faulty monostable 3/2 NC valve activated by a push-button.
- Study a faulty double acting cylinder with Reed sensors.
- Study a faulty bistable 5/2 valves with pneumatic activation.
- Study a faulty 5/3 closed center valve with pneumatic activation.
- Study a faulty vacuum pad with ejector.
- Study a faulty silencer for 6 mm tubing.
AE-PLC-PAN-UB (also available with others PLCmanufacturers):
- Activation of a simple effect cylinder with PLC.
- Activation of a double effect cylinder with PLC.
- Electro-pneumatic control by a monostable 3/2 NC solenoid valve activated from PLC.
- Electro-pneumatic control by monostable 3/2 and 5/2 solenoid valve activated from PLC.
- Electro-pneumatic control by a bistable 5/2 solenoid valve activated from PLC.
- Pressure control with PLC.
- Position control of a double effect cylinder using Reed sensors and a PLC.
- Creation a pneumatic sequence with the PLC.
The practices available with the AE-PLC-PAN-UB working alone are:
- Using variables.
- Using digital inputs I.
- Using digital inputs II.
- Testing digital inputs (PLC-PAN-K1).
- Using digital outputs.
- Testing digital outputs.
- Using analog signals I (PLC-PAN-K1 and PLC-PAN-K2).
- Using analog signals II (PLC-PAN-K1 and PLC-PAN-K2).
- Square wave generator.
- HMI simple program (PLC-PAN-K3 or PLC-PAN-K4).
- Using digital outputs with HMI device I (PLC-PAN-K3 or PLCPAN-K4).
- Using digital outputs with HMI device II (PLC-PAN-K3 or PLCPAN-K4).
- Reading data from a register with the HMI device (PLC-PAN-K3 or PLC-PAN-K4).
- Writing data to a register with the HMI device (PLC-PAN-K3 or PLC-PAN-K4).
- Switching screens of the HMI device (PLC-PAN-K3 or PLC-PAN-K4).
- Internet connection of the PLC unit (PLC-PAN-K5).
- Control digital inputs with a web server application (PLC-PAN-K5).
- Control digital outputs with a web server application (PLC-PAN-K5).
- Control analog inputs with a web server application (PLC-PAN-K5).
- Control analog outputs with a web server application (PLC-PAN-K5).
AE-PLC-SIE-UB (also available with others PLC manufacturers):
- Activation of a simple effect cylinder with PLC.
- Activation of a double effect cylinder with PLC.
- Electro-pneumatic control by a monostable 3/2 NC solenoid valve activated from PLC.
- Electro-pneumatic control by monostable 3/2 and 5/2 solenoid valve activated from PLC.
- Electro-pneumatic control by a bistable 5/2 solenoid valve activated from PLC.
- Pressure control with PLC.
- Position control of a double effect cylinder using Reed sensors and a PLC.
- Creation a pneumatic sequence with the PLC.
The practices available with the AE-PLC-SIE-UB working alone are:
- Using variables.
- Using digital inputs I.
- Using digital inputs II.
- Testing digital inputs (PLC-SIE-K1).
- Using digital outputs.
- Testing digital outputs.
- Using analog signals I (PLC-SIE-K1 and PLC-SIE-K2).
- Using analog signals II (PLC-SIE-K1 and PLC-SIE-K2).
- Square wave generator.
- HMI simple program (PLC-SIE-K3 or PLC-SIE-K4).
- Using digital outputs with HMI device I (PLC-SIE-K3 or PLC-SIE-K4).
- Using digital outputs with HMI device II (PLC-SIE-K3 or PLC-SIE-K4).
- Reading data from a register with the HMI device (PLC-SIE-K3 or PLC-SIE-K4).
- Writing data to a register with the HMI device (PLC-SIE-K3 or PLC-SIE-K4).
- Switching screens of the HMI device (PLC-SIE-K3 or PLC-SIE-K4).
- Internet connection of the PLC unit (PLC-SIE-K5).
- Control digital inputs with a web server application (PLC-SIE-K5).
- Control digital outputs with a web server application (PLC-SIE-K5).
- Control analog inputs with a web server application (PLC-SIE-K5).
- Control analog outputs with a web server application (PLC-SIE-K5).
AE-PLC-AB-UB (also available with others PLC manufacturers):
- Activation of a simple effect cylinder with PLC.
- Activation of a double effect cylinder with PLC.
- Electro-pneumatic control by a monostable 3/2 NC solenoid valve activated from PLC.
- Electro-pneumatic control by monostable 3/2 and 5/2 solenoid valve activated from PLC.
- Electro-pneumatic control by a bistable 5/2 solenoid valve activated from PLC.
- Pressure control with PLC.
- Position control of a double effect cylinder using Reed sensors and a PLC.
- Creation a pneumatic sequence with the PLC.
The practices available with the AE-PLC-AB-UB working alone are:
- Using variables.
- Using digital inputs I.
- Using digital inputs II.
- Testing digital inputs (PLC-AB-K1).
- Using digital outputs.
- Testing digital outputs.
- Using analog signals I (PLC-AB-K1 and PLC-AB-K2).
- Using analog signals II (PLC-AB-K1 and PLC-AB-K2).
- Square wave generator.
- HMI simple program (PLC-AB-K3 or PLC-AB-K4).
- Using digital outputs with HMI device I (PLC-AB-K3 or PLC-AB-K4).
- Using digital outputs with HMI device II (PLC-AB-K3 or PLC-AB-K4).
- Reading data from a register with the HMI device (PLC-AB-K3 or PLC-AB-K4).
- Writing data to a register with the HMI device (PLC-AB-K3 or PLC-AB-K4).
- Switching screens of the HMI device (PLC-AB-K3 or PLC-AB-K4).
- Internet connection of the PLC unit (PLC-AB-K5).
- Control digital inputs with a web server application (PLC-AB-K5).
- Control digital outputs with a web server application (PLC-AB-K5).
- Control analog inputs with a web server application (PLC-AB-K5).
- Control analog outputs with a web server application (PLC-AB-K5).
AE-PLC-OMR-UB (also available with others PLC manufacturers):
- Activation of a simple effect cylinder with PLC.
- Activation of a double effect cylinder with PLC.
- Electro-pneumatic control by a monostable 3/2 NC solenoid valve activated from PLC.
- Electro-pneumatic control by monostable 3/2 and 5/2 solenoid valve activated from PLC.
- Electro-pneumatic control by a bistable 5/2 solenoid valve activated from PLC.
- Pressure control with PLC.
- Position control of a double effect cylinder using Reed sensors and a PLC.
- Creation a pneumatic sequence with the PLC.
The practices available with the AE-PLC-OMR-UB working alone are:
- Using variables.
- Using digital inputs I.
- Using digital inputs II.
- Testing digital inputs (PLC-OMR-K1).
- Using digital outputs.
- Testing digital outputs.
- Using analog signals I (PLC-OMR-K1 and PLC-OMR-K2).
- Using analog signals II (PLC-OMR-K1 and PLC-OMR-K2).
- Square wave generator.
- HMI simple program (PLC-OMR-K3 or PLC-OMR-K4).
- Using digital outputs with HMI device I (PLC-OMR-K3 or PLCOMR-K4).
- Using digital outputs with HMI device II (PLC-OMR-K3 or PLCOMR-K4).
- Reading data from a register with the HMI device (PLC-OMR-K3 or PLC-OMR-K4).
- Writing data to a register with the HMI device (PLC-OMR-K3 or PLC-OMR-K4).
- Switching screens of the HMI device (PLC-OMR-K3 or PLC-OMR-K4).
- Internet connection of the PLC unit (PLC-OMR-K5).
- Control digital inputs with a web server application (PLC-OMR-K5).
- Control digital outputs with a web server application (PLC-OMR-K5).
- Control analog inputs with a web server application (PLC-OMR-K5).
- Control analog outputs with a web server application (PLC-OMR-K5).
AE-PLC-MIT-UB (also available with others PLC manufacturers):
- Activation of a simple effect cylinder with PLC.
- Activation of a double effect cylinder with PLC.
- Electro-pneumatic control by a monostable 3/2 NC solenoid valve activated from PLC.
- Electro-pneumatic control by monostable 3/2 and 5/2 solenoid valve activated from PLC.
- Electro-pneumatic control by a bistable 5/2 solenoid valve activated from PLC.
- Pressure control with PLC.
- Position control of a double effect cylinder using Reed sensors and a PLC.
- Creation a pneumatic sequence with the PLC.
The practices available with the AE-PLC-MIT-UB working alone are:
- Using variables.
- Using digital inputs I.
- Using digital inputs II.
- Testing digital inputs (PLC-MIT-K1).
- Using digital outputs.
- Testing digital outputs.
- Using analog signals I (PLC-MIT-K1 and PLC-MIT-K2).
- Using analog signals II (PLC-MIT-K1 and PLC-MIT-K2).
- Square wave generator.
- HMI simple program (PLC-MIT-K3 or PLC-MIT-K4).
- Using digital outputs with HMI device I (PLC-MIT-K3 or PLC-MIT-K4).
- Using digital outputs with HMI device II (PLC-MIT-K3 or PLC-MIT-K4).
- Reading data from a register with the HMI device (PLC-MIT-K3 or PLC-MIT-K4).
- Writing data to a register with the HMI device (PLC-MIT-K3 or PLC-MIT-K4).
- Switching screens of the HMI device (PLC-MIT-K3 or PLC-PAN-K4).
- Internet connection of the PLC unit (PLC-MIT-K5).
- Control digital inputs with a web server application (PLC-MIT-K5).
- Control digital outputs with a web server application (PLC-MIT-K5).
- Control analog inputs with a web server application (PLC-MIT-K5).
- Control analog outputs with a web server application (PLC-MIT-K5).
- Several other exercises can be done and designed by the user.
What is this?
These percentage scores are an average of 0 user reviews. To get more into detail, see each review and comments as per below
If you have used this product, support the community by submitting your review