Flexible Manufacturing System 1 (AE-PLC-FMS1)
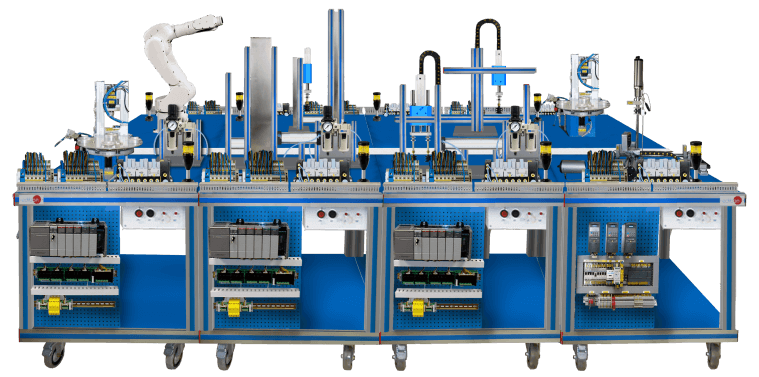

PL-727102
The Flexible Manufacturing System 1, “AE-PLC-FMS1,” by EDIBON is a modular automation system comprising several key workstations, including the Feeding Workstation for Pieces “AE-PLC-A,” Mounting Workstation “AE-PLC-M,” Automatic Pressing Workstation “AE-PLC-P,” Rotary Table Workstations “AE-PLC-MR1” and “AE-PLC-MR2,” Automatic Screw Workstation “AE-PLC-AT,” Robotic Arm Workstation “AE-BR,” Storage Workstation “AE-PLC-AL,” and Linear Transport Workstation “AE-PLC-T.”
The AE-PLC-FMS1 system automates the assembly process by supplying a base part and mounting multiple components onto it, followed by screwing and finally storing the assembled piece in a designated storage area. Here is an overview of the process sequence:
- Feeding Workstation: This station prepares the base parts with the correct dimensions and positions them on the linear transport system.
- Mounting Workstation: Another component is added to the base piece after a verification check, and it is then positioned on the transport system.
- Pressing Workstation: A hydraulic cylinder presses the newly mounted component into the base piece.
- Rotary Table Workstations: These two stations each add unique pieces of various colors, sizes, and materials to the base piece.
- Automatic Screw Workstation: Four screws are placed into the base piece.
- Robotic Arm Workstation: The robotic arm installs an automatic screwing tool to secure the screws into the mounted components.
- Storage Workstation: Finally, an automated manipulator transports the assembled part to its designated position in storage.
Each workstation operates autonomously via a local PLC, while a central PLC oversees coordination across the system. Communication between workstations and the central PC is established through an Ethernet protocol.
Designed to support the learning of automation fundamentals, the AE-PLC-FMS1 system offers practical training in areas such as PLC programming, Ethernet network operation, and technologies like pneumatics, electro-pneumatics, and vacuum systems. The optional “AE-AS” software allows students to practice real-world automation software skills through 2D and 3D process simulations, SCADA system supervision and control, PLC programming, and hydraulic, pneumatic, and electronic device simulations.
- AE-PLC-FMS1. Unit:
*Available PLC models of different manufacturers: PANASONIC, SIEMENS, OMRON, MITSUBISHI, ALLEN BRADLEY, etc.
- AE-PLC-PAN-UB. PANASONIC PLC Base Unit.
- N-ALI02. Domestic Power Supply.
- N-CPU-PAN. Panasonic CPU Module.
- PLC-PAN-K1, PANASONIC PLC Kit 1 (Optional).
- N-MT. Test module.
- PLC-PAN-K2, PANASONIC PLC Kit 2 (Optional).
- N-ESA-PAN. Panasonic Analog I/O Module.
- N-SWT-4.4 Ports Ethernet Switch Module.
- PLC-PAN-K4, PANASONIC PLC Kit 4 (Optional).
- N-HMIA-PAN. Panasonic Large HMI Module.
- N-SWT-4. 4 Ports Ethernet Switch Module.
- PLC-PAN-K5, PANASONIC PLC Kit 5 (Optional).
- N-MOD. Modem Communication Module.
- N-SWT-8. 8 Ports Ethernet Switch Module.
- AE-AS. Automation Systems Simulation Software. (Optional).
The complete unit includes as well:
- Advanced Real-Time SCADA.
- Open Control + Multicontrol + Real-Time Control.
- Specialized EDIBON Control Software based on LabVIEW.
- National Instruments Data Acquisition board.
- Calibration exercises, which are included, teach the user how to calibrate a sensor and the importance of checking the accuracy of the sensors before taking measurements.
- Projector and/or electronic whiteboard compatibility allows the unit to be explained and demonstrated to an entire class at one time.
- Capable of doing applied research, real industrial simulation, training courses, etc.
- Remote operation and control by the user and remote control for EDIBON technical support, are always included.
- Totally safe, utilizing 4 safety systems (Mechanical, Electrical, Electronic and Software).
- Designed and manufactured under several quality standards.
- Optional ICAI software to create, edit and carry out practical exercises, tests, exams, calculations, etc. Apart from monitoring user’s knowledge and progress reached.
- This unit has been designed for future expansion and integration. A common expansion is the EDIBON Scada-Net (ESN) System which enables multiple students to simultaneously operate many units in a network.
- PLC, HMI and web server programming software.
- Component Workstations.
- SAC. Silent Air Compressor Unit
- HPU. Hydraulic Power Unit
- Cables and Accessories, for normal operation.
- Manuals: This unit is supplied with 8 manuals. Required services, Assembly and Installation, Interface and Control software, Starting-up, Safety, Maintenance, Calibration and Practices manuals.
EXERCISES AND PRACTICAL POSSIBILITIES TO BE DONE WITH THE MAIN ITEMS
- Introduction to flexible manufacturing system (FMS).
- Introduction to pneumatics and electro-pneumatics.
- Introduction to vacuum technology.
- Study of the sensor detection.
- Testing the digital inputs and outputs of the automatic system through a PLC.
- Modify manufacturing parameters through the PLC.
- Configuration of a pneumatic application.
- Introduction to the Human-machine interface systems (HMI).
- Study of an automatic control of an industrial system.
- Control of the flexible manufacturing system through a central PLC in an Ethernet network with local PLC in each workstation.
- Manage the flexible manufacturing system through the HMI device.
What is this?
These percentage scores are an average of 0 user reviews. To get more into detail, see each review and comments as per below
If you have used this product, support the community by submitting your review