IIOT Based Smart Factory Setup with Industrial Robot (Smart Factory)
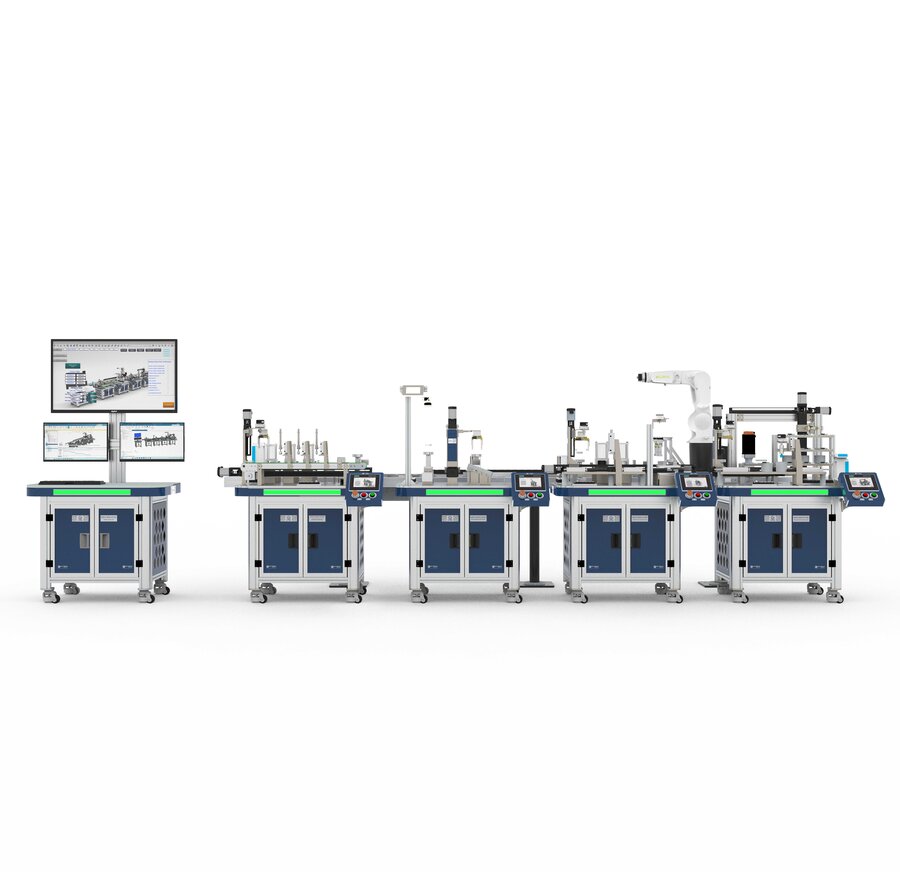

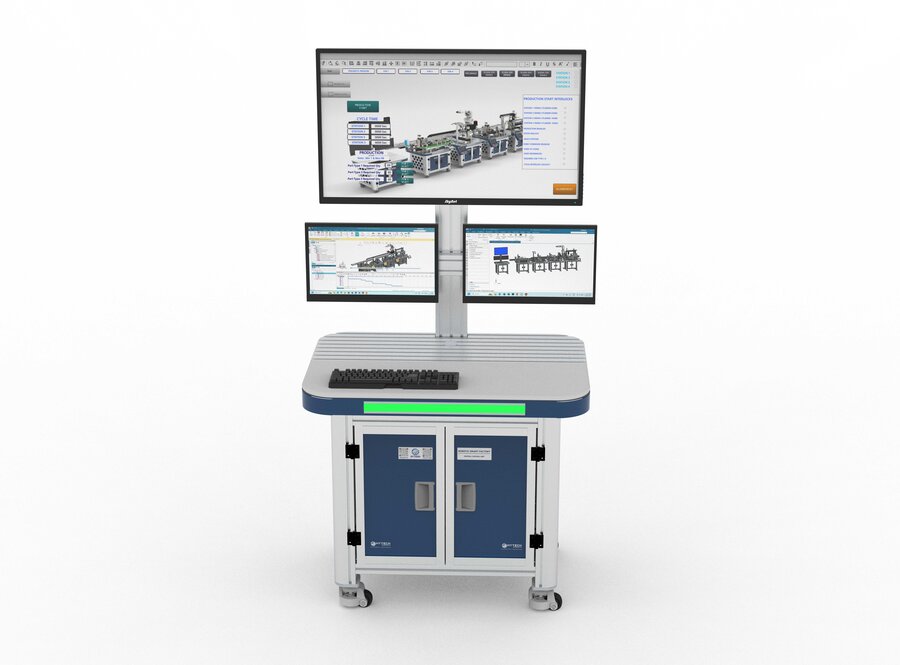
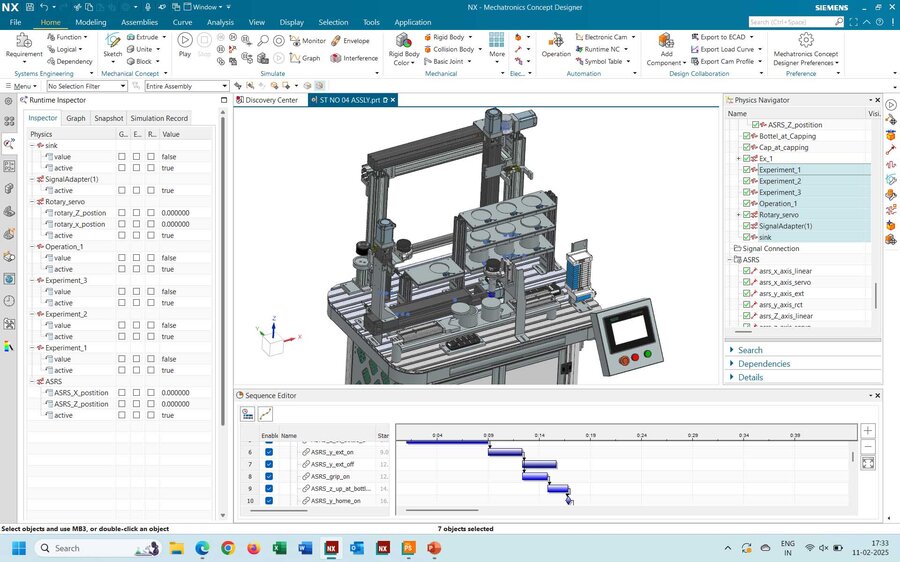
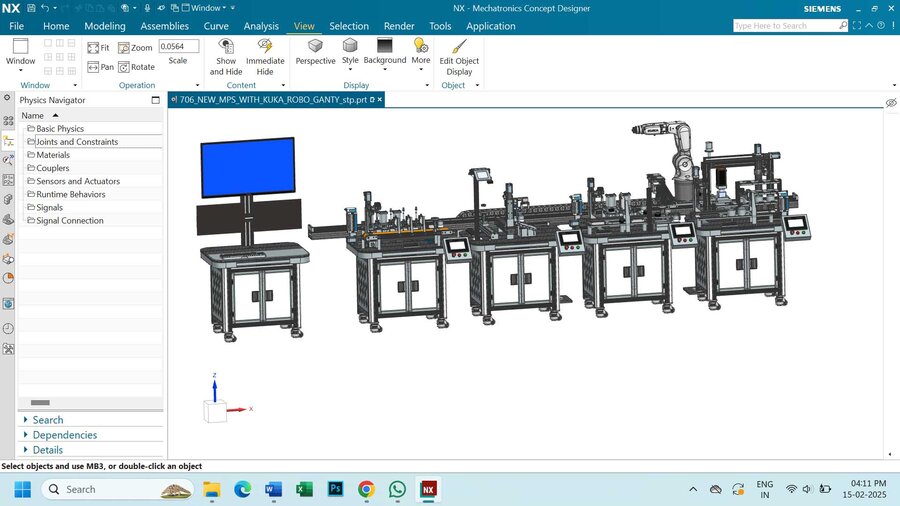
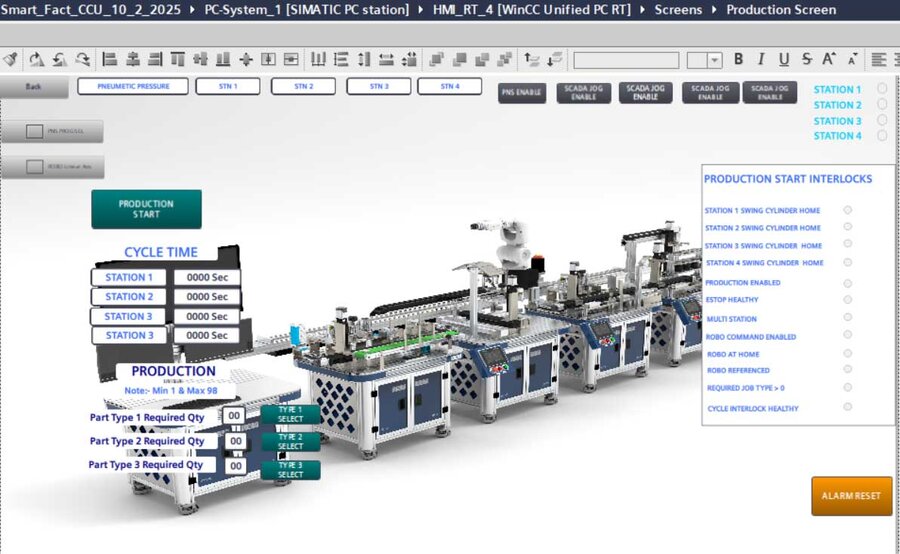
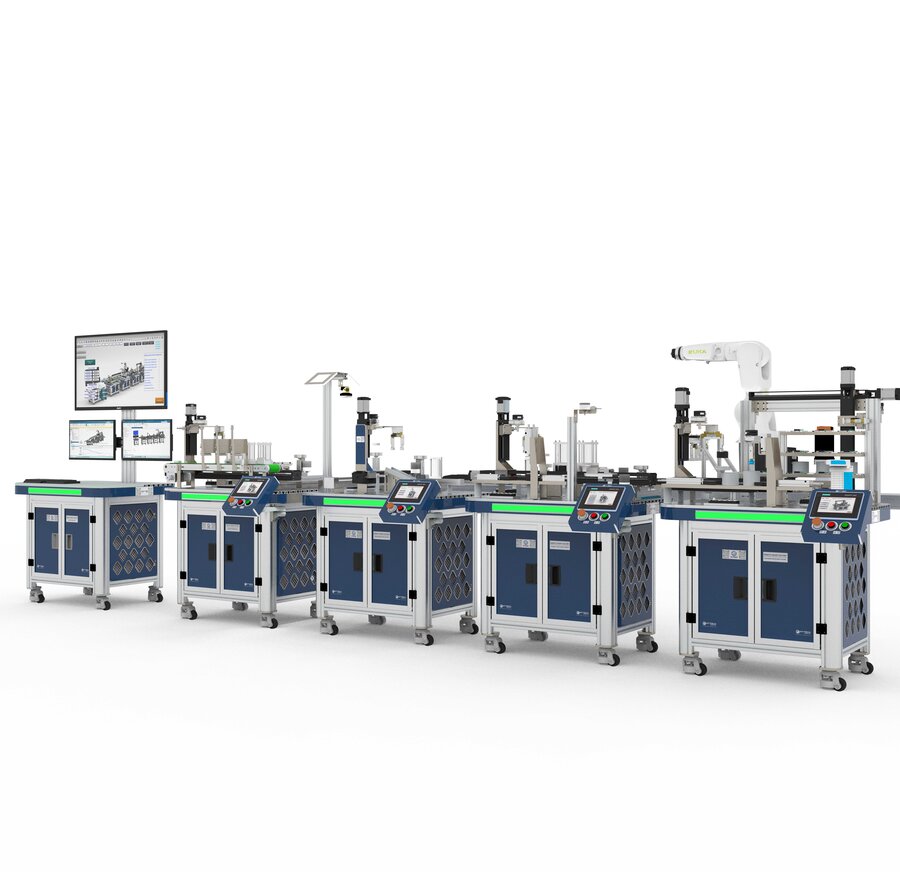
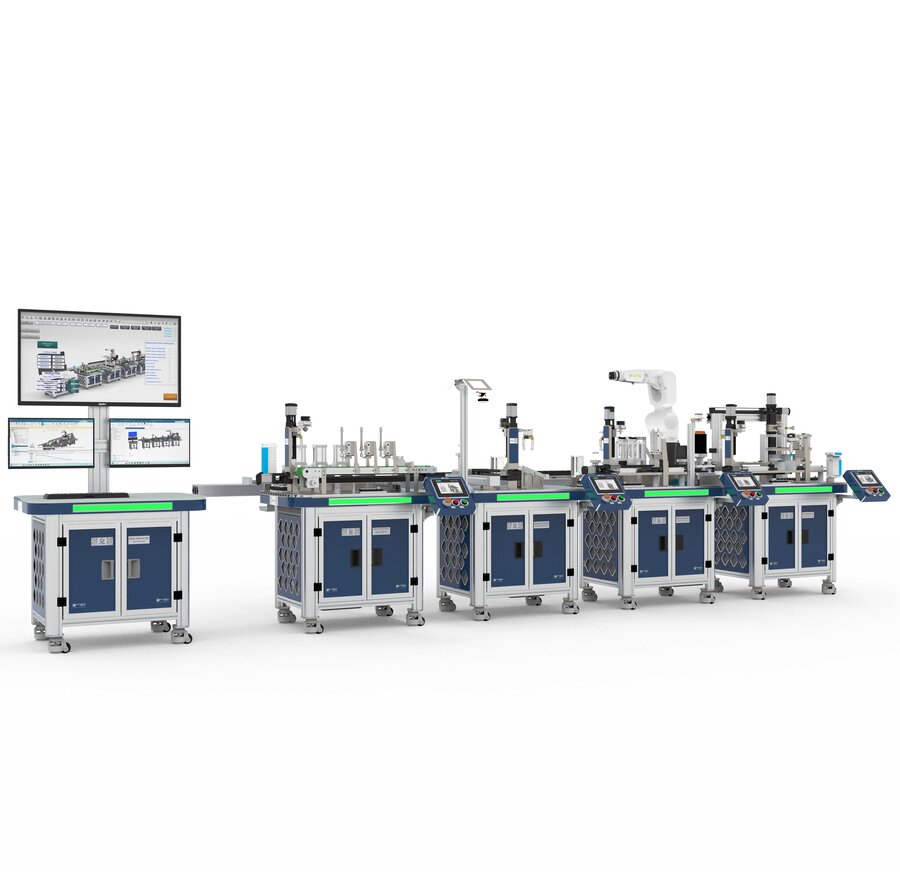
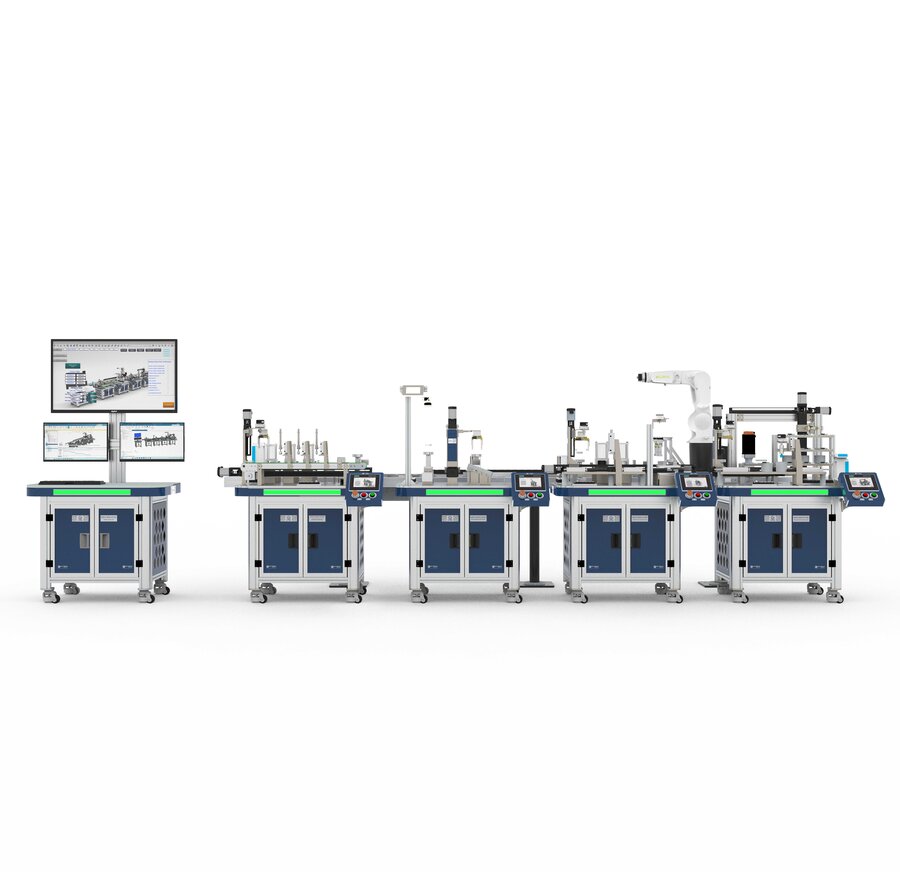
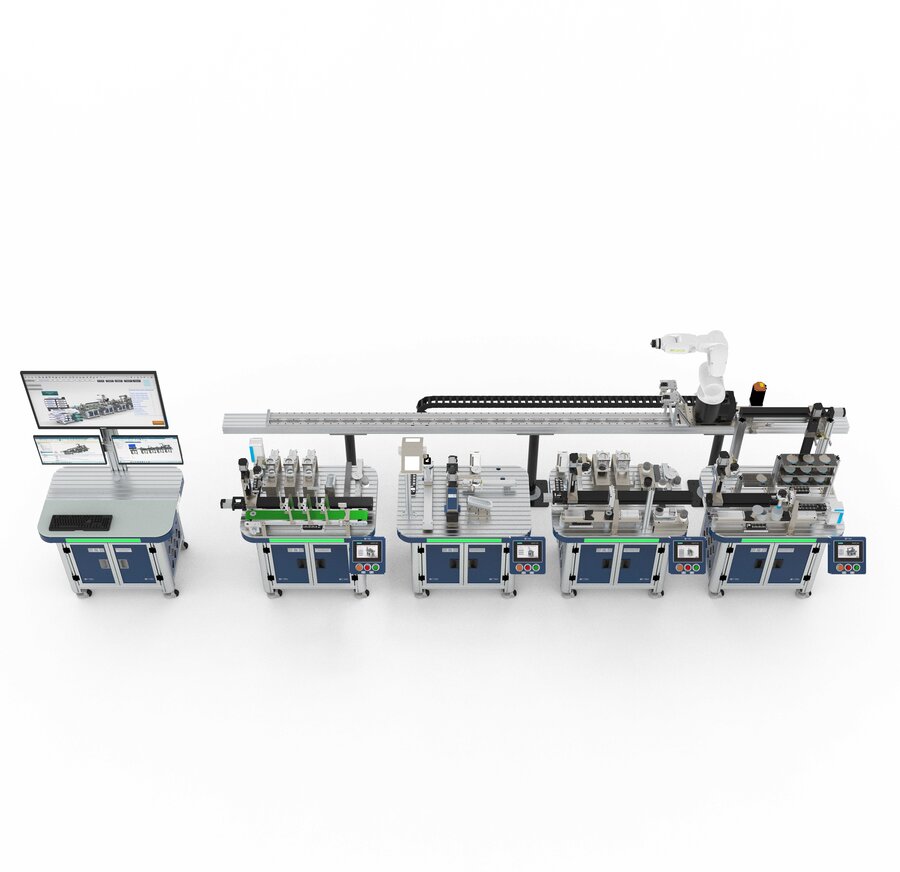
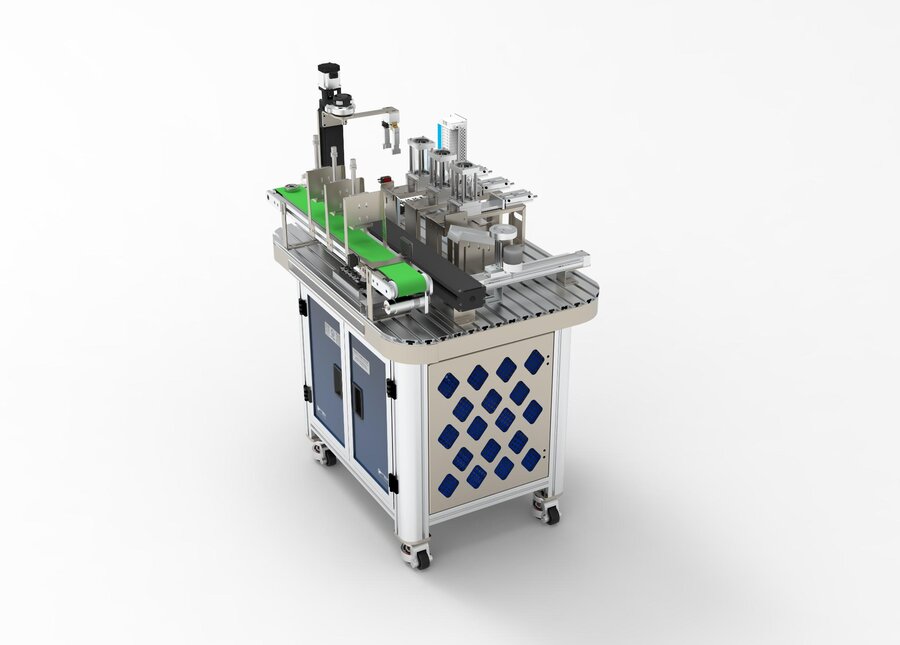
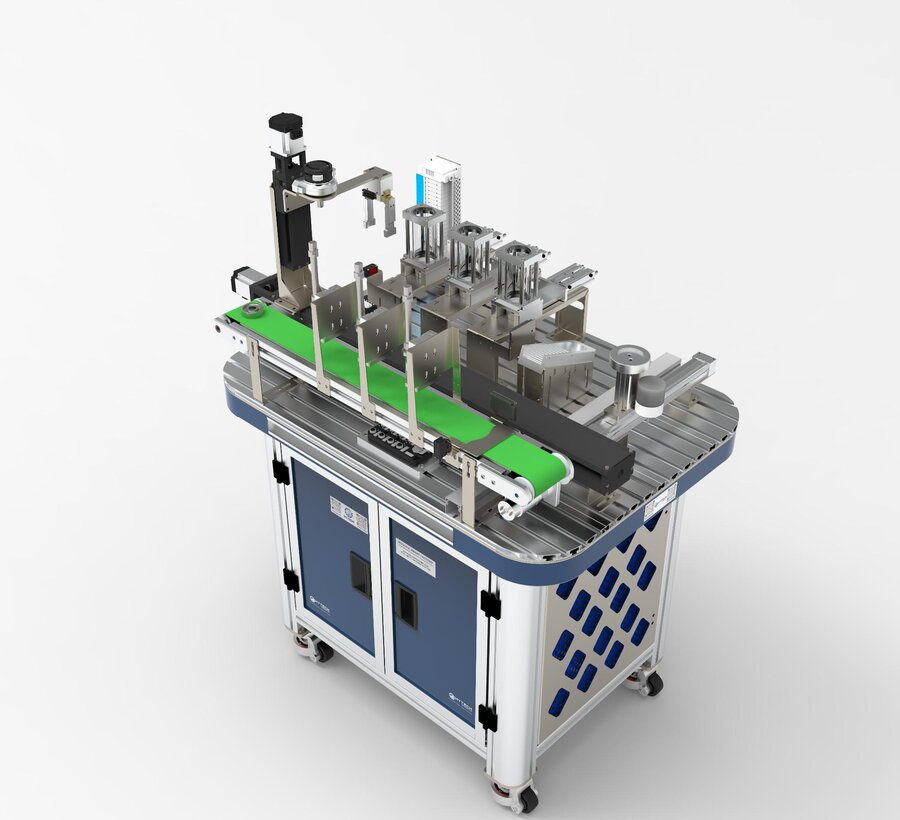
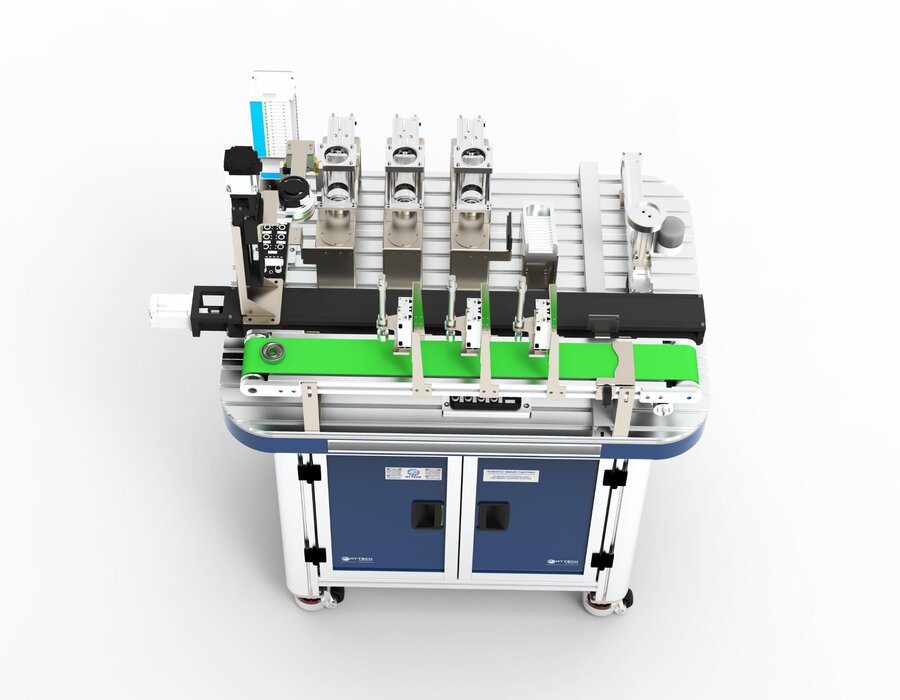
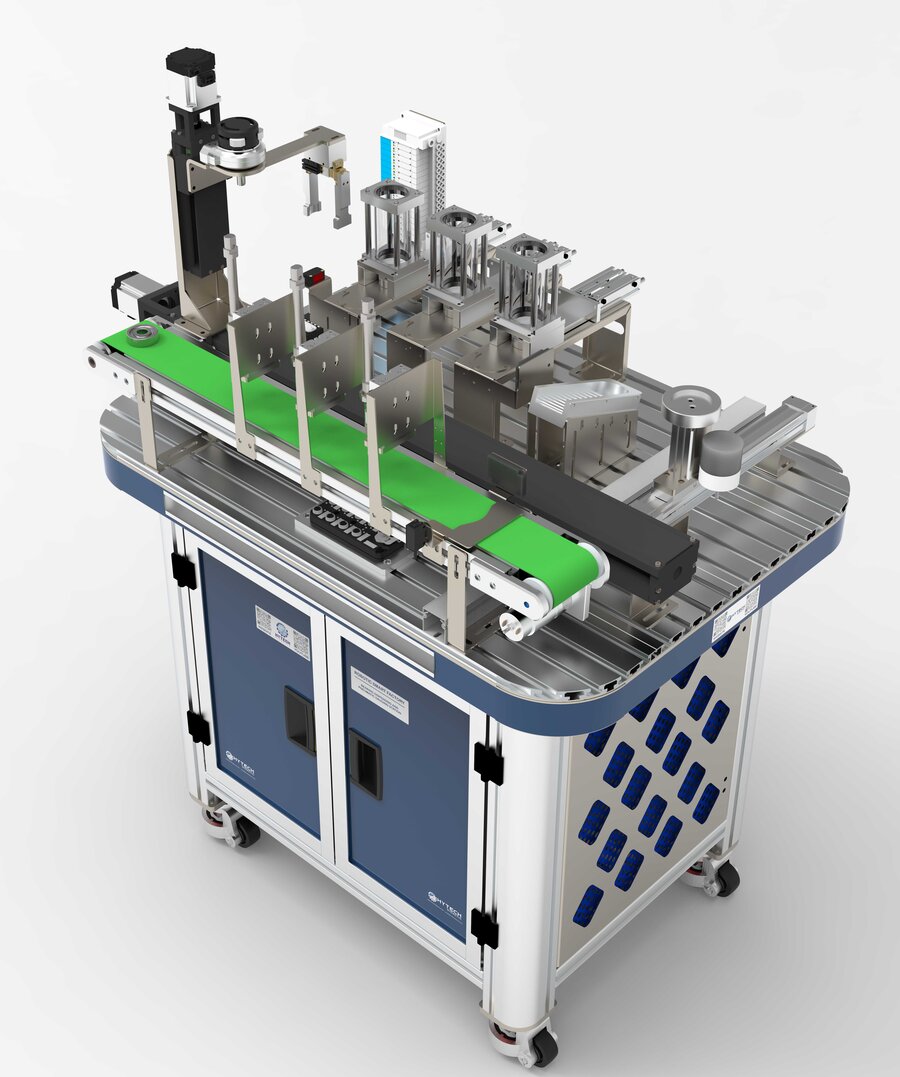
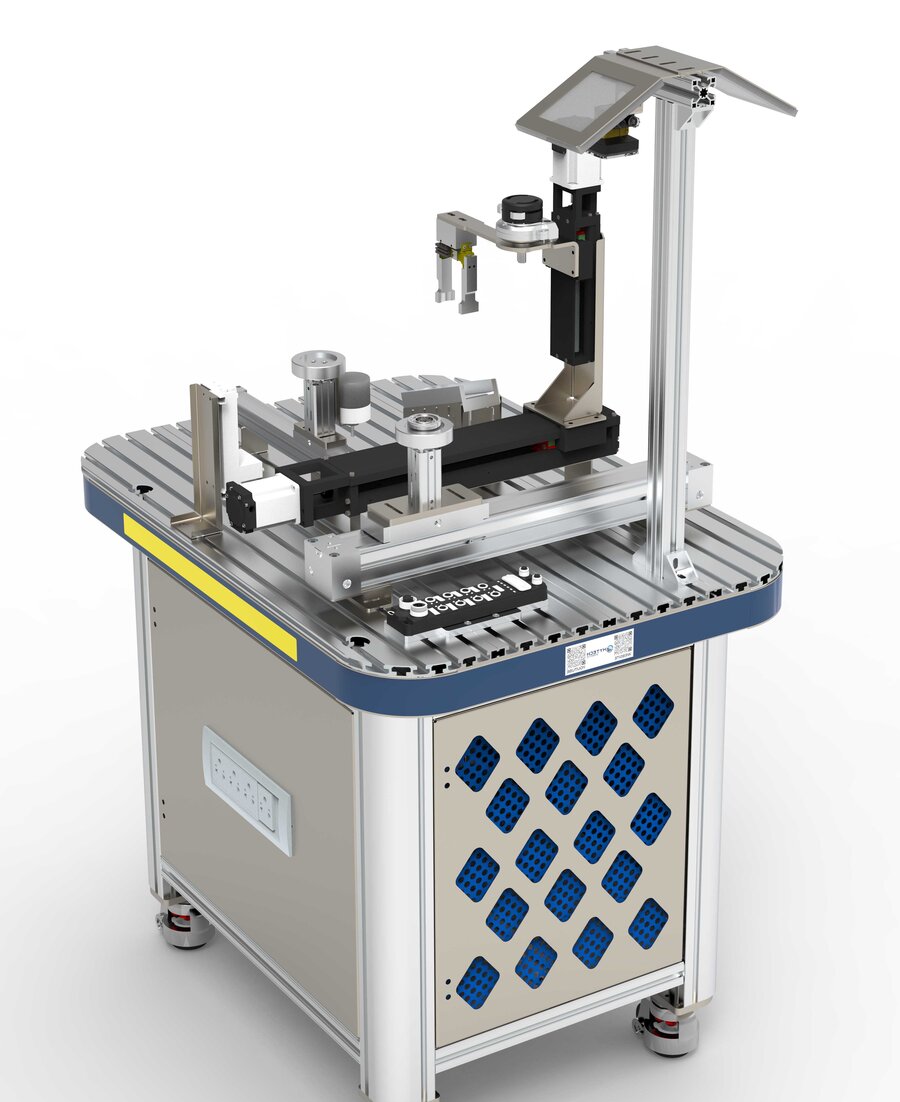
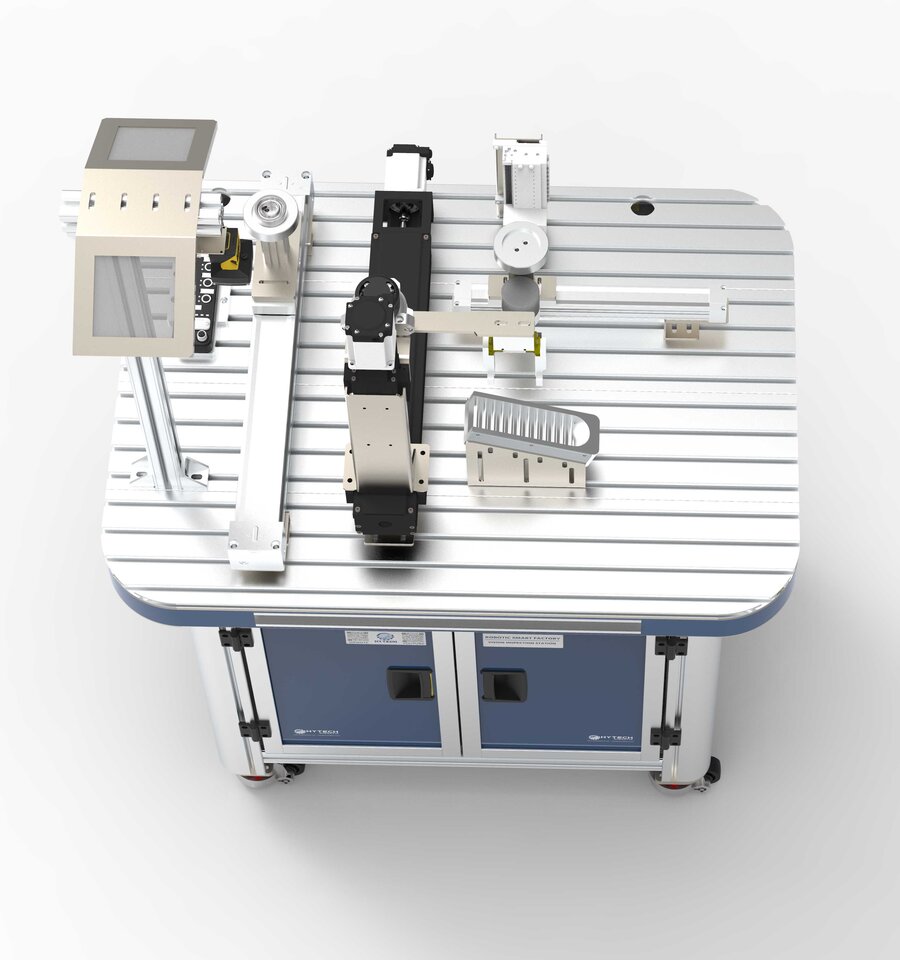
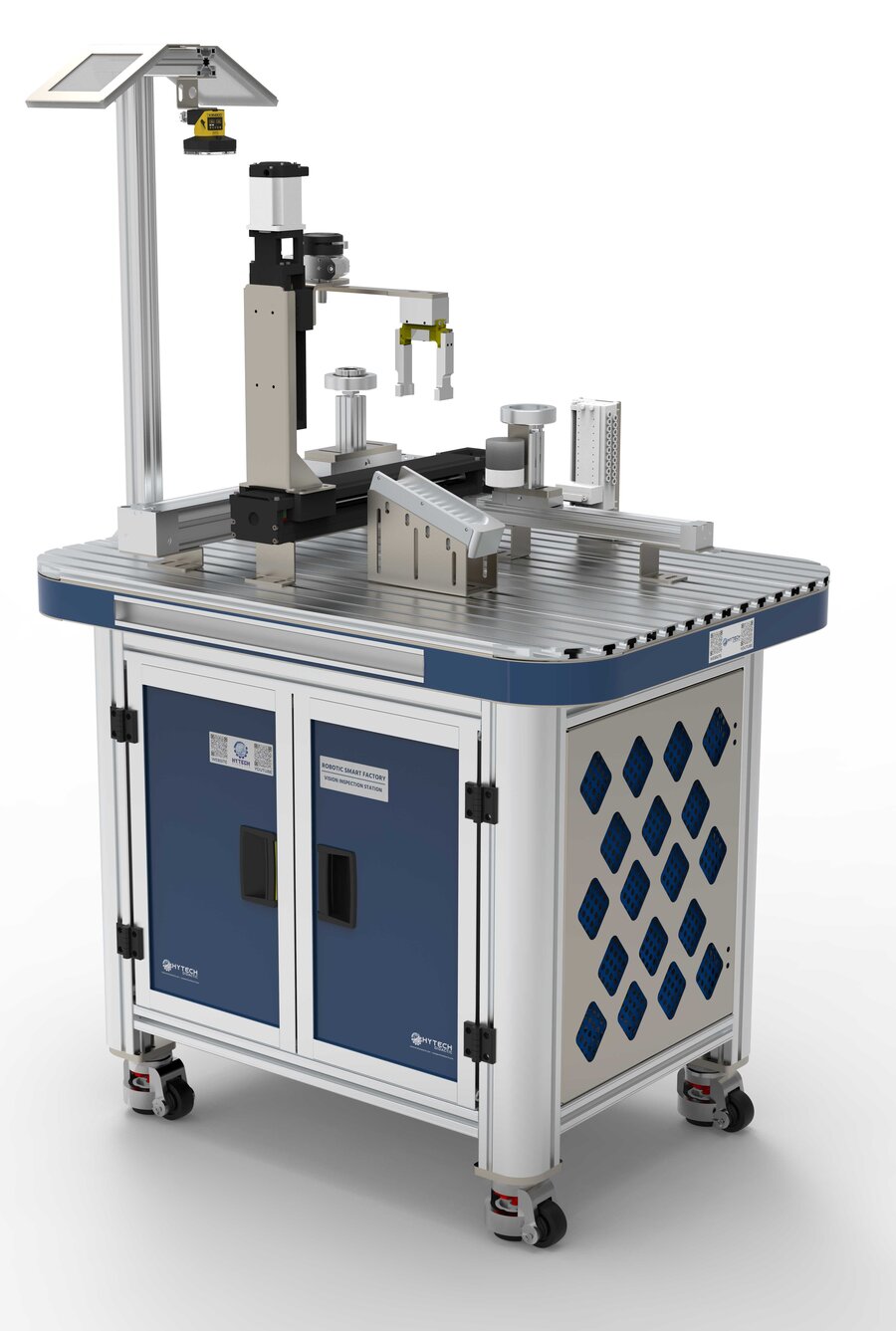
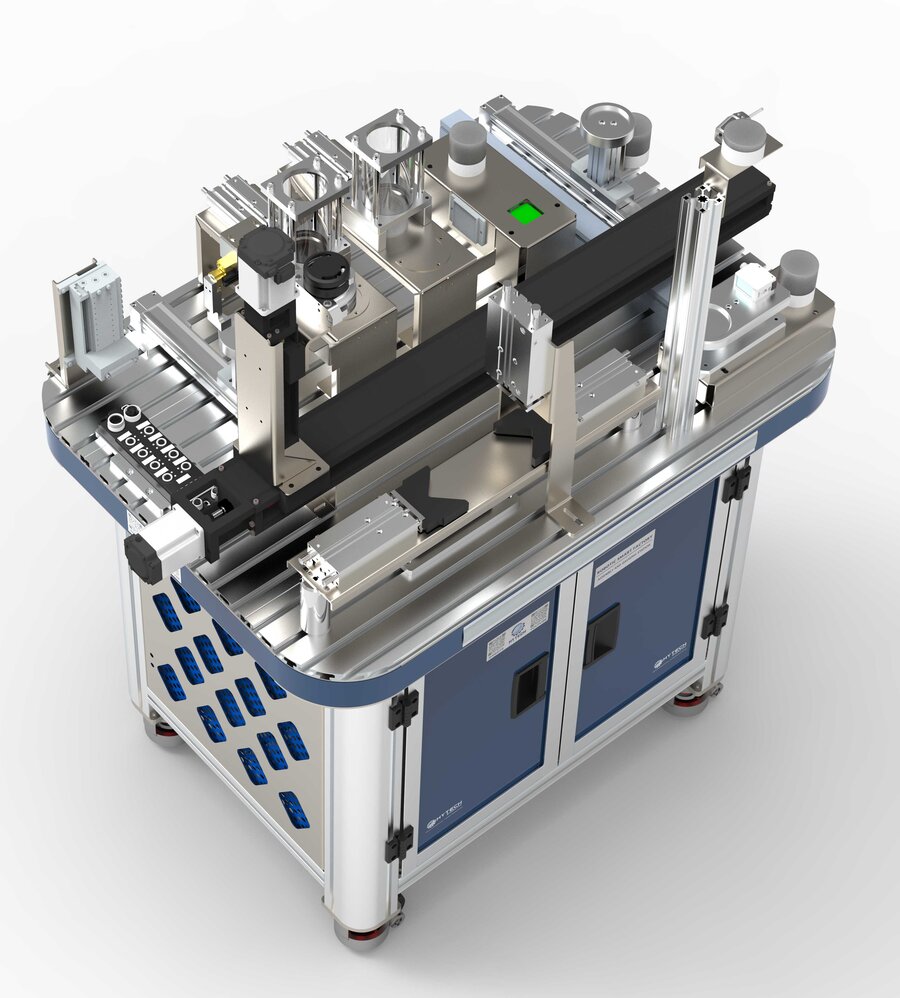
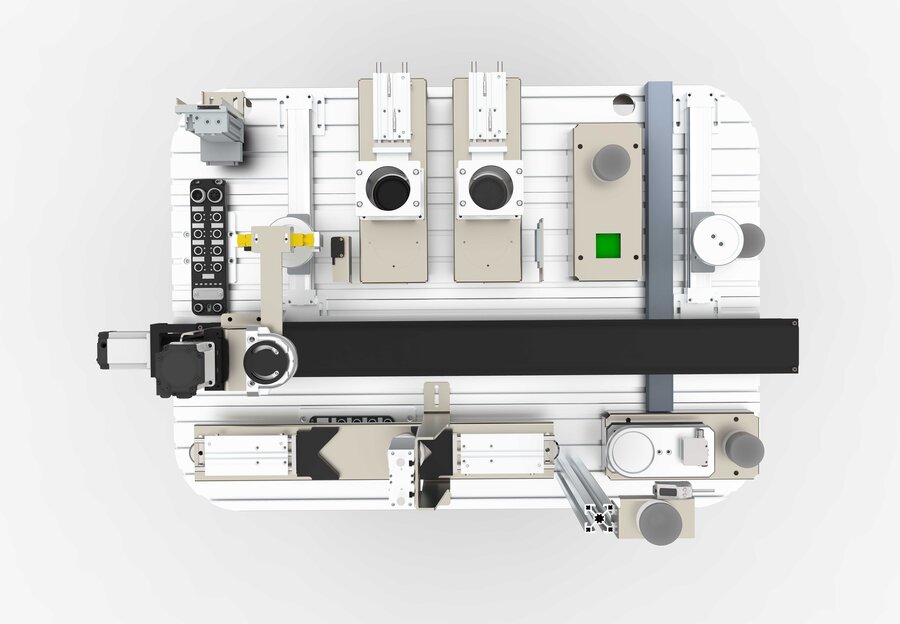
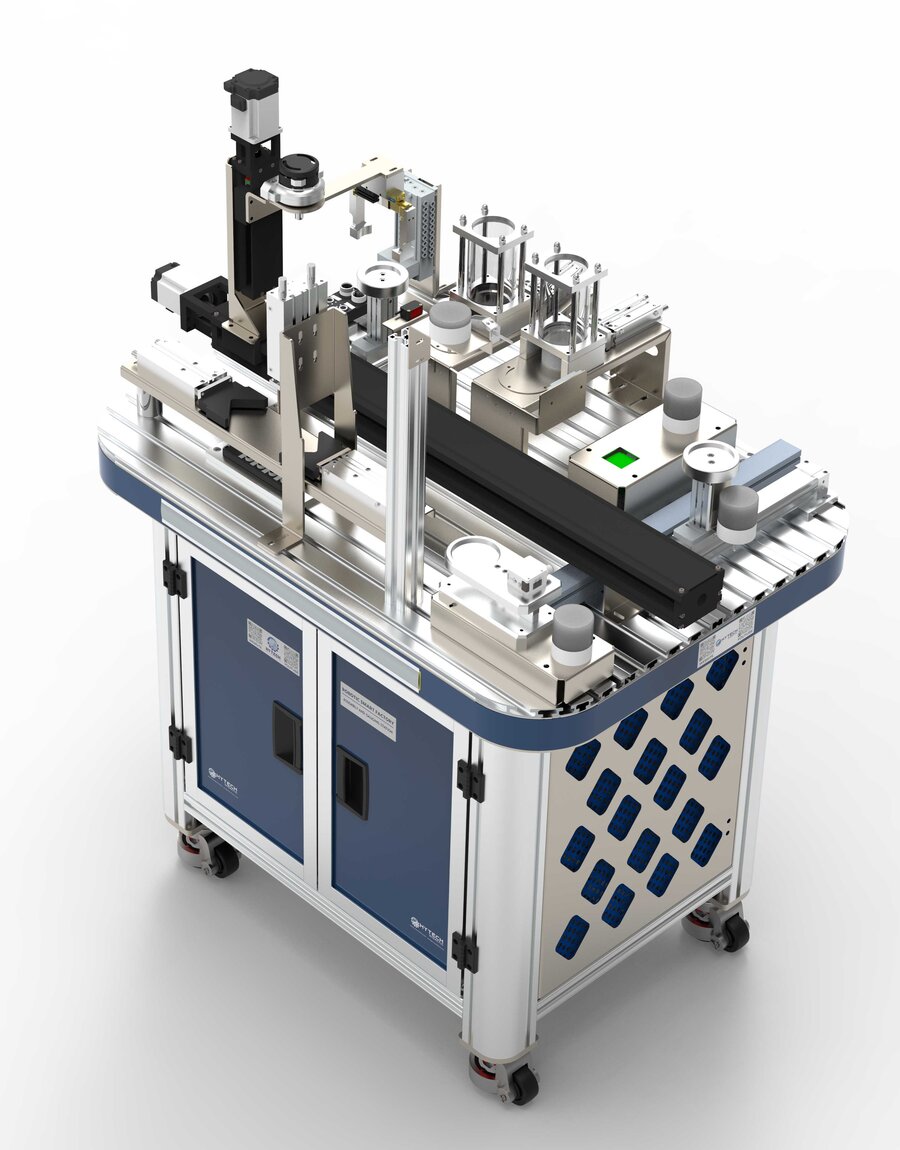
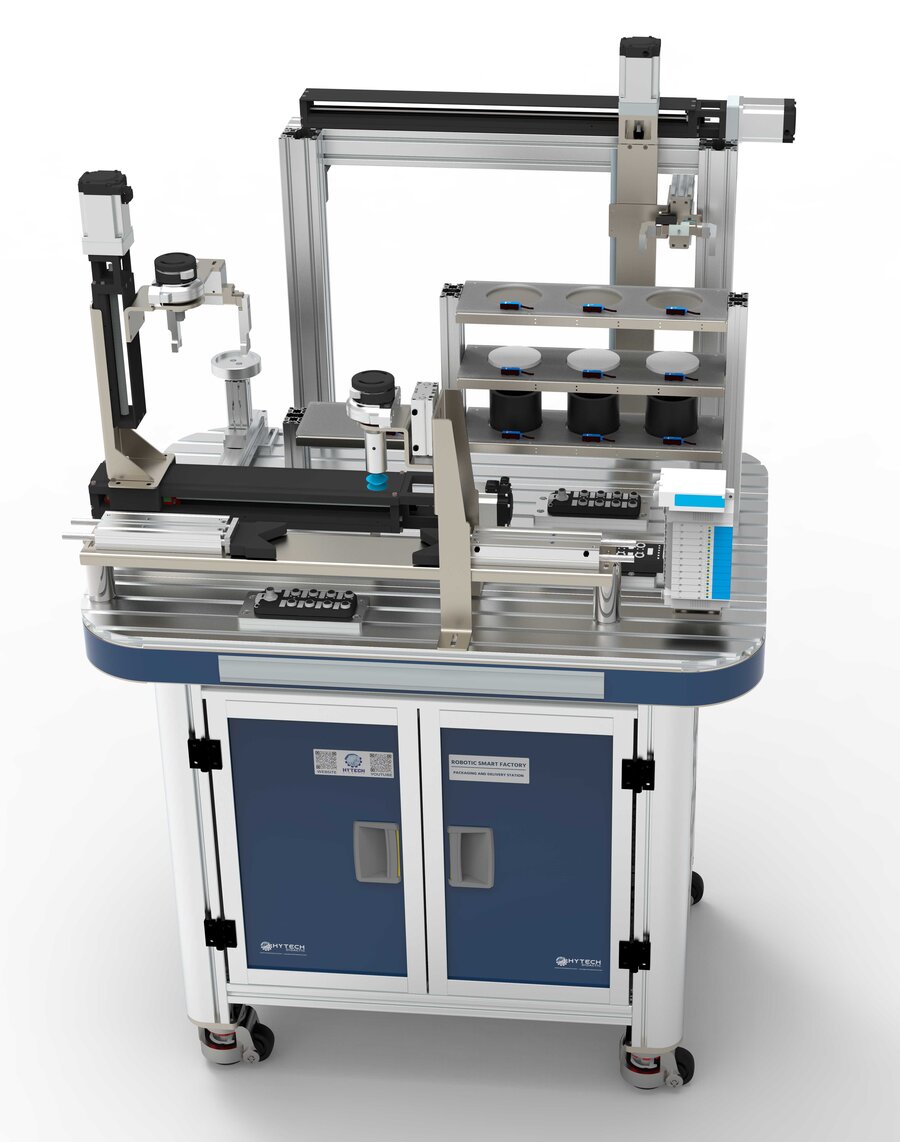
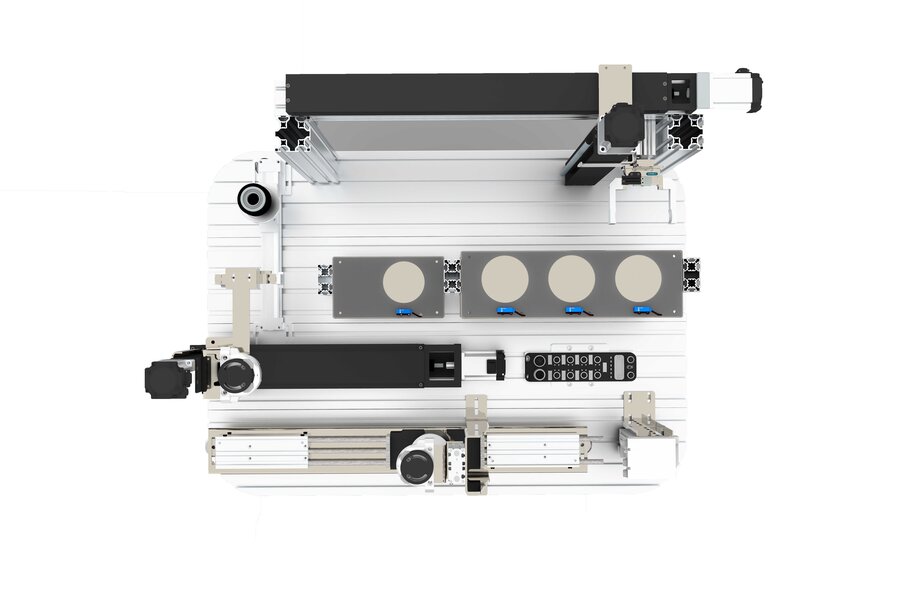
PL-988015
Key Features of the Robotic Smart Factory 1. Seamless Industrial Integration • Fully integrated with PLC, HMI, SCADA, and IIoT Edge technologies for an immersive Industry 4.0 training experience. • Incorporates IO-Link-based master modules, enabling real-time device-level communication and modular system expansion. • Supports RFID tracking, sensor data logging, and real-time decision-making across all stations. 2. Advanced Station-Specific Functionalities • Each station is designed for distinct automation tasks using real-world components: • Station 1: Pneumatic gauging with high-accuracy diameter classification and automated rejection. • Station 2: Vision-based inspection with classification, defect detection, and sorting via smart camera. • Station 3: Assembly with integrated weight measurement, color sensing, and level detection. • Station 4: ASRS-based material handling with vacuum-based capping and rotary pick-and-place. • Encourages learners to explore complete industrial workflows—from part identification to final packaging. 3. Gantry-Mounted 7th Axis Robot with Automatic Tool Changer • High-precision robot mounted on a gantry system enables inter-station part handling over extended travel ranges. • Equipped with a smart tool changer, enabling automatic switching between grippers and tools based on process needs. 4. Immersive Digital Twin Integration • Fully integrated with digital twin software, enabling: • Real-time simulation of all robotic and material handling operations. • Safe virtual testing of logic and sequences before deployment. • Parallel training of multiple users for collaborative learning environments. 5. Virtual Programming & Simulation Tools • Includes offline programming utilities for robot path planning and PLC/HMI logic validation. • Minimizes risk of hardware damage and optimizes commissioning time by detecting errors in the virtual phase. 6. Rugged and Modular Hardware Design • Framework constructed using industrial-grade aluminum extrusions for longevity and easy configuration. • Each module includes: • Transparent polycarbonate enclosures ensuring 360° visibility and enhanced safety. • Anti-static industrial work surfaces and high-durability component mounting. • Lockable castor wheels for mobility and stability in lab environments. 7. Centralized Intelligent Control System • Features a dedicated control panel equipped with: • Industrial PLC (e.g., Siemens/Mitsubishi) for automation control. • Touch-based HMI interface for operator-friendly interaction. • SCADA-enabled monitoring and diagnostics for real-time system insights. 8. Fully Equipped Operator Workstation • Delivered with a pre-installed software suite for: • Digital twin operations and visualization. • Offline robot and PLC programming. • Real-time HMI/SCADA interaction and process monitoring.
Industrial Robot with Automatic Tool Changer Flexible Automation for Multi-Tasking Operations The Industrial Robot with Tool Changer is a high-performance robotic solution designed to perform multiple operations by automatically switching between different tools. This setup enhances flexibility, efficiency, and adaptability in manufacturing environments. Key Features: • Automatic Tool Changing System: Enables seamless switching between tools (e.g., grippers, screwdrivers, welders) without manual intervention. • Multi-Axis Robotic Arm: High-precision, repeatable motion for handling complex tasks. • Compact Tool Storage Rack: Secure placement of various end-effectors for quick access. • Integrated with PLC & HMI: Ensures smooth coordination and real-time monitoring. • Smart Sensors & Safety Features: Equipped with position sensors, interlocks, and safety controls for reliable operation. Station 1: Bearing Dispensing and Pneumatic Gauging Station Station 1 is equipped with a pneumatic gauging system that sorts three different types of bearings with the same outer diameter but varying inner diameters. Any bearing other than the three predefined types will be rejected at Station 1. Learning outcomes • PLC and HMI Integration • Integration of Reed switches with PLC • Integration of Sensor with PLC • Sequential Operations of PLC • Gauging Operation with Reed Switch Feedback • PLC integration with Servo system • Quality-based sorting and decision-making logic • Operation of Pneumatic Solenoid Valves (Profinet Communication) in integration • PLC and HMI • PLC and SCADA robot integration. Sation 2: Vision Inspection Station Station 2 is equipped with a vision inspection system. The vision camera inspects each bearing based on predefined teaching parameters. If a bearing does not meet these parameters, it will be rejected. The system sorts three types of bearings, while rejected items are placed in a designated bin. Learning outcomes: • PLC and HMI Integration • Sequential Operations of PLC • PLC Integration with vision sensor • Vision camera Teaching • Application and operation of Rodless cylinder • Operation of Pneumatic Solenoid Valves (Profinet Communication) in integration with PLC and HMI. • PLC integration with Servo system • Pneumatic rotary operation • Servo positions- Absolute, Relative and homing of position. • Robot integration with PLC and SCADA Station 3: Assembly and Gauging Station In this station, the bearing housing is dispensed from the bearing dispensing module and positioned on the sensing modules, where its weight is measured both before and after assembly. A color sensor identifies the bearing housing's color and level sensor measures its depth. The bearing housing is then assembled with the bearing, and the assembled product is transferred to the RFID module. In the RFID module, the system detects the tag attached to the bearing housing, and the PLC records its weight, color, and level. Finally, the bearing housing is transferred to the storing and packaging station. Learning outcomes • Understand basic PLC hardware components. • PLC and HMI Integration. • Principle and operation of Color Sensor. • Application of color sensor in automation system. • Principle and operation of Weight Sensor. • Application of Weight Sensor in automation system. • Principle and operation of Level Sensor. • Application of Level Sensor in automation system. • Integration of Level Sensor with plc. • Integration of Weight Sensor with plc. • Integration of Level Sensor with plc. • Functions and applications of RFID Sensor • Integration of RFID sensor with PLC • RFID system for real-time data write and Read • PLC and SCADA robot integration Station 4: Packaging and Storage Station The ASRS Cartesian robot retrieves a container and cap from the ASRS storage rack. The servo motor-based rotary pick-and-place module picks up the container and cap from the ASRS storage rack and transfers them to the Capping Module. In the Capping Module, the container cap is securely fixed onto the container using a vacuum-based suction mechanism. After capping, the system transfers the capped container back to the ASRS storage rack. Learning Outcomes • PLC and HMI Integration • Understand basic PLC hardware components • Operation of Pneumatic Solenoid Valves (Profinet Communication) in integration with PLC and HMI. • PLC integration with Servo system • Pneumatic rotary and gripper operation • Servo positions and teaching • ASRS operation and applications Central Control with PLC – HMI and IIOT 1. Centralized Control with PLC and HMI Integration o The robotic training cells feature a separate Central Control Unit comprising a PLC (Programmable Logic Controller) and HMI (Human-Machine Interface). o Robots are seamlessly integrated with the PLC and HMI, enabling trainees to operate complete robotic cycles within an industrial automation context. o This setup provides comprehensive exposure to industrial robotic architecture and hands-on experience with state-of-the-art robotics. 2. Customization and Experimentation o Users can design and implement various PLC programs and develop custom HMI screens for controlling robot operations. o Trainees can experiment with diverse industrial automation components, such as: RFID Reader/Writer: For tracking and automation applications. Color Sensors: For detecting and responding to color variations in automated workflows. IO-Link Sensors: Such as color, distance, and proximity sensors for high-resolution part tracking and condition-based control. Servo & Pneumatic Actuators: For movement control in dispensing, assembly, and robotic handling tasks. o These components are integrated with the robot via the PLC-HMI framework, providing real-world automation scenarios. 3. Industrial IoT (IIoT) Integration o Siemens Industrial Edge technology is incorporated to offer advanced IIoT capabilities. o Trainees gain essential skills in data collection, analysis, and remote monitoring—key aspects of modern industrial environments. 4. Comprehensive Licensing o All required software licenses for PLC, HMI, and Industrial Edge are pre-installed and fully operational. o The workstation included with the setup ensures a seamless and efficient training experience. Learning Outcomes • Understand the Role of CCU • Integration and Control of RTU (7th Axis of Robot) • SCADA Design and Implementation • Digital Twin Integration via OPC UA • Comprehensive Smart Factory Operation Gantry-Mounted Robot System with Tool Changer Flexible Material Handling Across Smart Factory Stations High-Precision Gantry Integration • Features a robot mounted on a linear gantry (7th axis) that enables extended reach and mobility across multiple factory stations. • The gantry is constructed using rigid aluminum extrusions and equipped with high-accuracy servo-driven linear motion, ensuring smooth and precise transfer of components between processes. Automatic Tool Changer • The robot is equipped with a pneumatic or servo-driven tool changer, enabling automatic switching between end-effectors based on task requirements. • Supports multiple tools such as: o Pneumatic grippers for bearing and component handling o Vacuum suction cups for container and cap pickup o Custom end tools for assembly and inspection tasks • Enhances operational flexibility and reduces cycle time by eliminating manual tool change interventions. PLC and HMI Controlled Operation • Fully controlled via central PLC and HMI, allowing dynamic programming of robot tasks and tool paths. • Users can monitor gantry positions, tool status, and part flow in real-time using integrated HMI/SCADA interfaces. Industrial IoT (IIoT) Integration Connecting Machines to Intelligence Our smart factory integrates Siemens Industrial Edge technology to enable real-time connectivity, data-driven insights, and intelligent automation. This IIoT-enabled environment equips trainees with cutting-edge skills in digital manufacturing and connected industry solutions. Key Features: • Siemens Industrial Edge: Bridges OT and IT by processing data directly at the machine level for faster decision-making. • Real-Time Data Acquisition: Captures operational data from sensors, PLCs, and machines. • Edge-to-Cloud Connectivity: Securely transfers relevant data to cloud platforms for deeper analytics. • Dashboard & Analytics Tools: Enables visualization of trends, performance metrics, and predictive insights. Training Highlights: • Learn to collect, process, and analyze industrial data from real-time sources. • Understand remote monitoring, condition-based maintenance, and production optimization. • Work with IIoT protocols such as MQTT, OPC UA, and edge computing concepts. • Prepare for Industry 4.0 roles in smart manufacturing environments. Robotic Smart factory Training cell (Learning Management System) Robotics Smart factory technology is an advanced and continuously evolving field. Training of trainers plays a pivotal role in equipping them to impart effective training to students. Hytech Robotics Smart factory training cells come equipped with a comprehensive Learning Management System (LMS) designed to enhance the learning experience. Key Features of the Hytech LMS: • Step-by-Step Guidance: Trainers receive a structured, step-by-step guide to understand various robotic technologies. • Up-to-Date Training Content: Courses within the LMS are continually upgraded to align with the latest advancements in robotics technology. • Customizable Content: Trainers can create their own training modules, conduct examinations, and issue certifications directly through the LMS. • Support for Management: The LMS is an invaluable tool for addressing trainer attrition and ensuring consistent training and handholding for trainers. Robotic Smart Factory Courses in the LMS: The Hytech LMS offers courses that focus on both theoretical knowledge and practical applications in Robotic Smart Factory. These courses are designed to build a strong foundation and enhance hands-on skills for trainers and students alike. Contact us today for a free demonstration of the Hytech LMS and explore how it can transform Robotic Smart Factory training at your institution.
What is this?
These percentage scores are an average of 0 user reviews. To get more into detail, see each review and comments as per below
If you have used this product, support the community by submitting your review