Computer Controlled Modular Control and Regulation Unit (RYC-T)
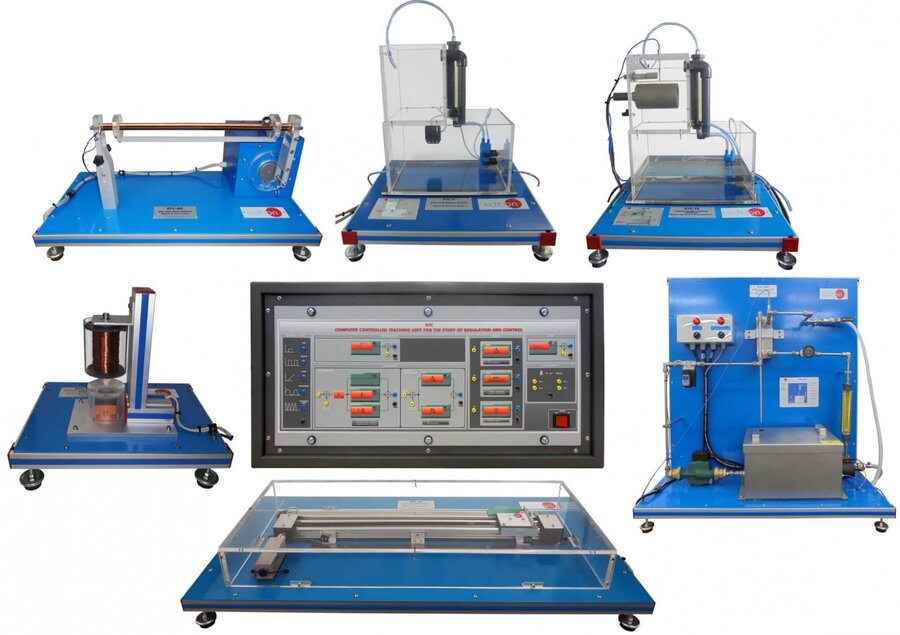

PL-563230
Control theory is broadly divided into two main areas: classical and modern. Classical control designs, such as PID controllers, are easier to implement than modern control methods, making them the preferred choice for most industrial applications.
The "RYC/T" Computer Controlled Modular Control and Regulation Unit by EDIBON allows students to simulate various systems, including an integrator, a first-order system, and a second-order system. These can be regulated using a PID controller or a Lead and Lag compensator, and the unit enables the addition of perturbations and offsets to analyze system responses.
The unit is compatible with various modules like the DC Servo Motor Module and the Ball and Beam Module, offering hands-on exploration of control system responses and real-time regulation studies. It is supplied with EDIBON's SCADA-based Computer Control System, which includes the unit itself, a Data Acquisition Board, and software for process control, data acquisition, and data management, enabling precise control and analysis of all process parameters.
- RYC. Unit:
- Metallic box.
- Diagram in the front panel with distribution of the elements similar to the real one.
- Reference signals module.
- PID controller module.
- Lead/Lag compensator:.
- Integrator system.
- First order system.
- Second order system.
- Perturbation module.
- Offset module.
- Analog Inputs.
The complete unit includes as well:
- Advanced Real-Time SCADA.
- Open Control + Multicontrol + Real-Time Control.
- Specialized EDIBON Control Software based on LabVIEW.
- National Instruments Data Acquisition board.
- Calibration exercises, which are included, teach the user how to calibrate a sensor and the importance of checking the accuracy of the sensors before taking measurements.
- Projector and/or electronic whiteboard compatibility allows the unit to be explained and demonstrated to an entire class at one time.
- Capable of doing applied research, real industrial simulation, training courses, etc.
- Remote operation and control by the user and remote control for EDIBON technical support, are always included.
- Totally safe, utilizing 4 safety systems (Mechanical, Electrical, Electronic and Software).
- Designed and manufactured under several quality standards.
- Optional ICAI software to create, edit and carry out practical exercises, tests, exams, calculations, etc. Apart from monitoring user’s knowledge and progress reached.
- This unit has been designed for future expansion and integration. A common expansion is the EDIBON Scada-Net (ESN) System which enables multiple students to simultaneously operate many units in a network.
- RYC/CCSOF. PID Computer Control + Data Acquisition + Data Management Software:
- Cables and Accessories, for normal operation.
- Manuals: This unit is supplied with the following manuals: Required services, Assembly and Installation, Interface and Control software, Starting-up, Safety, Maintenance, Calibration and Practices manuals.
EXERCISES AND PRACTICAL POSSIBILITIES TO BE DONE WITH THE MAIN ITEMS
- Response of a first order system in time domain. (Step response).
- Response of a first order system in time domain. (Ramp response).
- Response of a first order system in time domain. (Sine response).
- Response of a first order system in frequency domain. (Sine response).
- Response of a second order system in time domain. (Step response).
- Response of a second order system in time domain. (Ramp response).
- Response of a second order system in time domain. (Sine response).
- Response of a second order system in frequency domain. (Sine response).
- Phase Lead Compensator experiment.
- Phase Lag Compensator experiment.
- Structure of a PID controller. (Proportional-IntegrativeDerivative blocks).
- PID control of a first order system in open-loop.
- PID control of a second order system in open-loop.
- PID control of a first order system in closed-loop. (Mathematical tuning).
- PID control of a first order system in closed-loop. (Experimental tuning).
- PID control of a first order system in closed-loop. (ZieglerNichols tuning).
- PID control of a second order system in closed-loop. (Mathematical tuning).
- PID control of a second order system in closed-loop. (Experimental tuning).
- PID control of a second order system in closed- loop. (ZieglerNichols tuning).
What is this?
These percentage scores are an average of 0 user reviews. To get more into detail, see each review and comments as per below
If you have used this product, support the community by submitting your review