Computer Controlled Wind Energy Unit (EEEC)
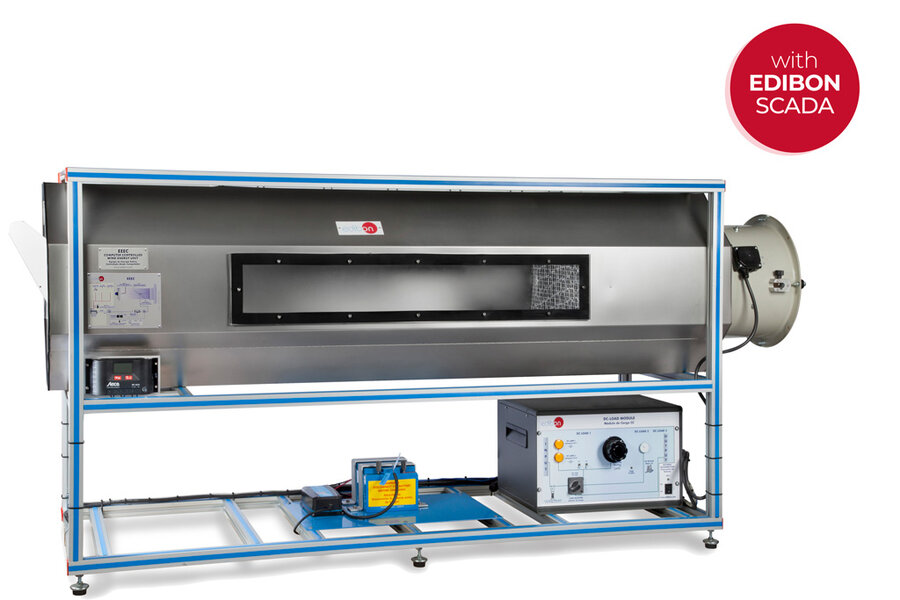

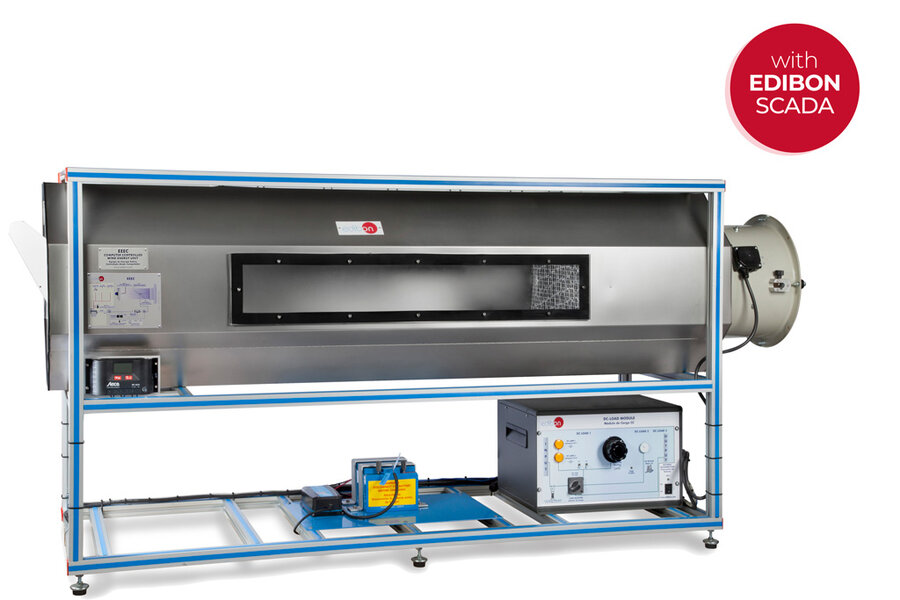
PL-263405
The "EEEC" Computer Controlled Wind Energy Unit is a laboratory-scale system that facilitates the study of kinetic wind energy conversion into electrical power and allows examination of various factors affecting this generation process. It features a stainless steel tunnel, an aerogenerator, and an axial fan with variable speed control, which is computer-operated. The main elements of the aerogenerator include a rotor, capable of holding multiple blades, and a generator that forms the core of the energy conversion system. The unit's fan speed can be adjusted, allowing the airflow to rotate the aerogenerator’s rotor, which in turn drives the generator to convert this kinetic energy into electricity.
With adjustable settings, the aerogenerator allows modification of the incidence angle and blade angle. The blades are removable, providing flexibility in blade configurations, which makes it possible to analyze their effects on energy efficiency and power output. The unit includes a DC load regulation system with an auxiliary battery charger, battery, and DC loads module, comprising lamps, rheostat, motor, load selector, and switches for various load selections. Sensors within the unit provide real-time measurement of critical parameters, including air temperature, airflow speed, rotor speed (rpm), voltage, and current. A temperature sensor before the rotor and an airflow sensor in the tunnel contribute to a comprehensive analysis of both environmental and performance variables. Additionally, voltage and current sensors measure power output, both before and after regulation, enabling precise assessments of efficiency and power.
Furthermore, the unit can determine the thrust force applied to the wind turbine in the direction of the wind and measure the mechanical torque during turbine operation. The EEEC unit is equipped with the EDIBON SCADA system, which includes the main unit, a Control Interface Box, Data Acquisition Board, and specialized software for process control, data acquisition, and monitoring of all operational parameters, supporting in-depth exploration and analysis of wind energy applications.
- EEEC. Unit:
- Anodized aluminum frame and panels made of painted steel.
- The unit includes wheels to facilitate its mobility.
- Main metallic elements made of stainless steel.
- Diagram in the front panel with distribution of the elements similar to the real one.
The unit includes
- Stainless steel tunnel.
- Aerogenerator.
- Computer controlled axial fan with variable speed for wind simulation.
- DC load regulator.
- Auxiliary battery charger.
- Battery.
- DC loads module.
- Sensors.
The complete unit includes as well:
- Advanced Real-Time SCADA.
- Open Control + Multicontrol + Real-Time Control.
- Specialized EDIBON Control Software based on LabVIEW.
- National Instruments Data Acquisition board.
- Calibration exercises, which are included, teach the user how to calibrate a sensor and the importance of checking the accuracy of the sensors before taking measurements.
- Projector and/or electronic whiteboard compatibility allows the unit to be explained and demonstrated to an entire class at one time.
- Capable of doing applied research, real industrial simulation, training courses, etc.
- Remote operation and control by the user and remote control for EDIBON technical support, are always included.
- Totally safe, utilizing 4 safety systems (Mechanical, Electrical, Electronic and Software).
- Designed and manufactured under several quality standards.
- Optional ICAI software to create, edit and carry out practical exercises, tests, exams, calculations, etc. Apart from monitoring user’s knowledge and progress reached.
- This unit has been designed for future expansion and integration. A common expansion is the EDIBON Scada-Net (ESN) System which enables multiple students to simultaneously operate many units in a network.
- EEEC/CIB. Control Interface Box.
- EEEC/CCSOF. Computer Control + Data Acquisition + Data Management Software.
- Cables and Accessories, for normal operation.
- Manuals: This unit is supplied with 8 manuals. Required services, Assembly and Installation, Interface and Control software, Starting-up, Safety, Maintenance, Calibration and Practices manuals.
EXERCISES AND PRACTICAL POSSIBILITIES TO BE DONE WITH THE MAIN ITEMS
- Identification and familiarization with all components of the unit and how they are associated with its operation.
- Familiarization with the regulator parameters and the wind energy measurements.
- Study of the conversion of kinetic wind energy into electrical energy.
- Study of the power generated by the aerogenerator depending on the wind speed.
- Determination of the typical parameters of the aerogenerator (short circuit current, open-circuit voltage, maximum power).
- Determination of the I-V curve.
- Study of voltage, current and power in function of different loads.
- Study of the influence of the load variation on the aerogenerator.
- Determination of the maximum power output of the aerogenerator.
- Determination of the P-air speed curve.
- Study of the power generated by the aerogenerator depending on the incident angle of the air.
- Study of the characteristic curve of the rotor.
- Study of the connection of loads to direct voltage.
What is this?
These percentage scores are an average of 0 user reviews. To get more into detail, see each review and comments as per below
If you have used this product, support the community by submitting your review