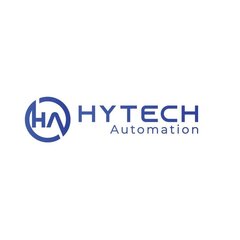
PA-689808
Hytech Automation
Focusing on CNC machines and training systems for industrial automation, electrohydraulics, electropneumatics, mechatronics and PLC since mid 1990s.
Country of origin
India
Founded
Hytech Automation
Support languages
English
Products listed on Edquip
9